08 - What is the “gain-in-weight” Method in the context of gravimetric asynchronous dosing?
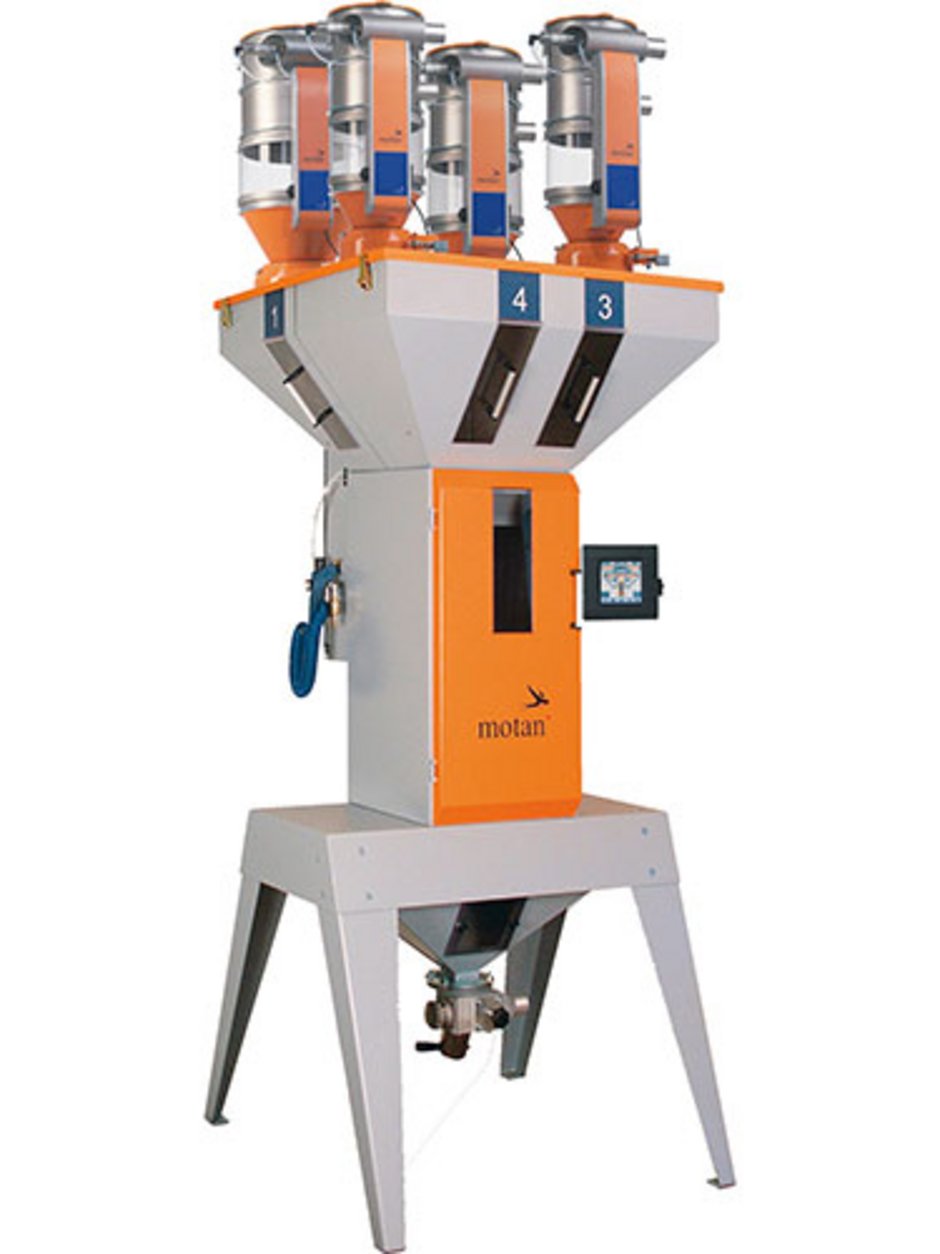
Gravimetric asynchronous dosing is also known as discontinuous or batch dosing.
As we explained in part 2, gravimetric systems weigh the ingredients before dosing, i.e. mass is the defining parameter.
The mass of the ingredients can be measured in two ways:
- Gain-in-weight systems measure the increase in aggregate mass in the weighing chamber as the material is being metered.
- Loss-in-weight systems measure the decrease in mass of the ingredients remaining in the supply hoppers.
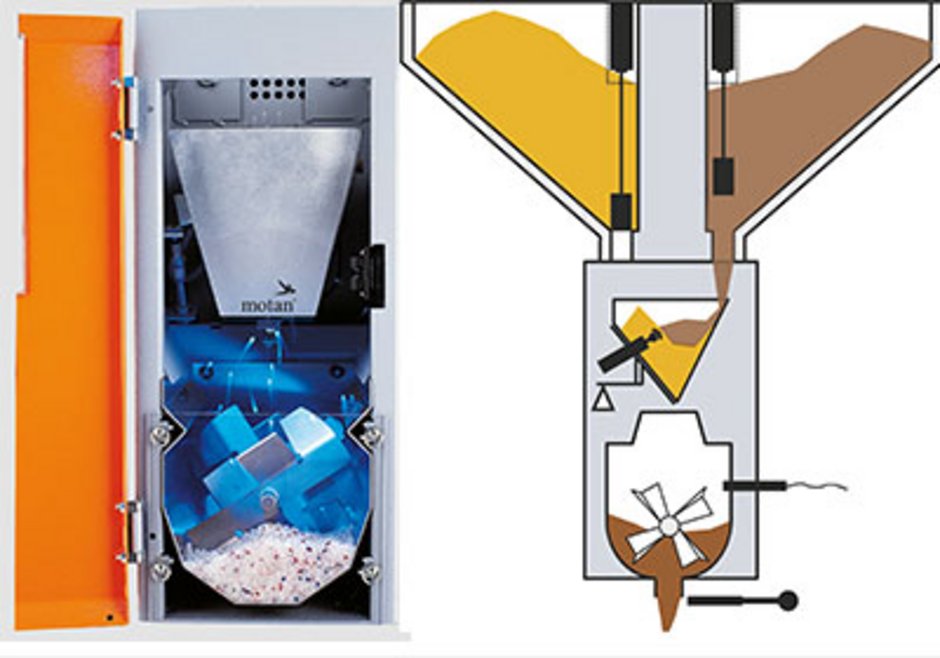
Gravimetric asynchronous units meter ingredients to the weighing chamber one after the other, to form a batch. The total mass in the weighing chamber is measured as each new component is added, in line with the quantities and ratios specified in the recipe. Ingredients are metered precisely using slide-gate valves, screws or disc dosing elements, for example.
Because the metered components form layers on top of one another, a mixer is required to actively blend the ingredients. The contents of the weighing chamber are fed to a separate downstream mixing chamber.
Depending on the system design, the material is then fed directly into the feed throat of an injection moulding machine, or for example, into a day bin.
Alternatively, there is the variation where all components except the main one are metered. This is frequently deployed for injection moulding machines for the addition of one or two ingredients (additives). In this method, the main component (granulate) is continuously fed into throat of the processing machine. However, you have no control over its flow rate.
The control system requires information on the shot- weight of the injection moulding machine. Based on this data, the system can calculate how much of each additive must be dosed.
The dosing cycle is triggered by a signal issued from the injection moulding machine.
Compared to metering all components, this method offers an advantage because it requires one less dosing module while maintaining the same standard of quality.
When it comes to mixing, the properties of the ingredients must be taken into account. Blending materials with different bulk densities can result in unwanted segregation. This can be partly prevented by switching the mixer on and off and running shorter mixing cycles.
The size of the mixing hopper is important to ensure sufficient time for effective blending of the recipe components over multiple cycles. As a result, the
maximum possible throughput of the dosing and mixing unit does not only depend on the capacity of the dosing modules but also on the size of the mixing hopper.
In the next issue, we will take a closer look at loss-in-weight dosing.
Sounds very theoretical to you? For dosing systems visit www.motan.com