68 - What are the criteria for choosing a dosing screw?
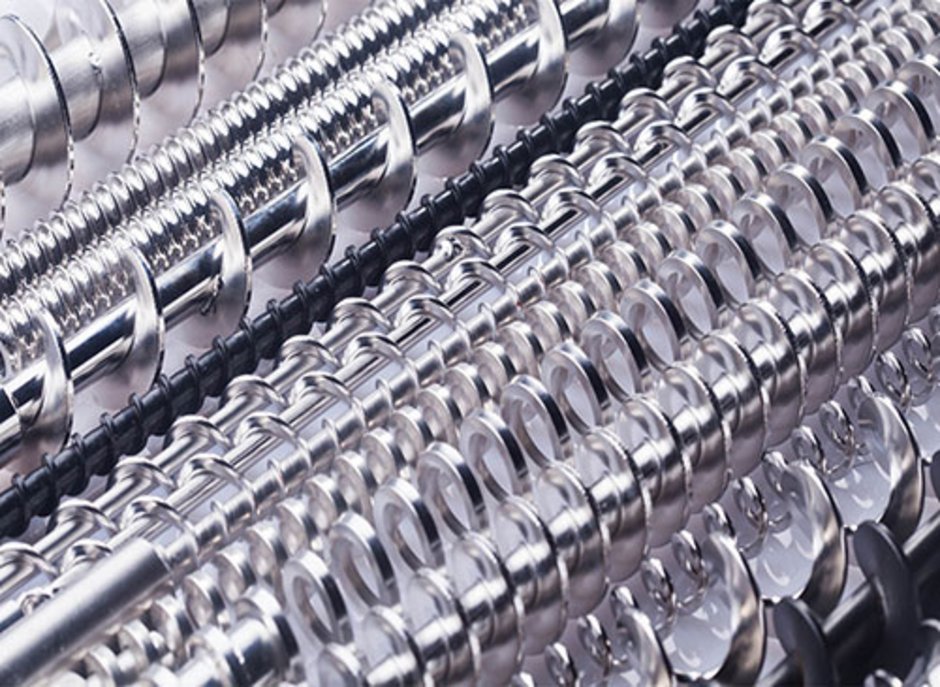
Choosing the correct dosing is the key to precise dosing. The dosing screw’s job is to transport bulk material evenly and consistently. For this to work, screw and dosing material need to be the correct fit. The type and shape of the bulk material (granulate, pellets, powder, fibres, flakes) play an important role, as do the specific material properties, for example whether it is free-flowing or non-free-flowing, bridge-building or whether it can be fluidized.
Other factors that influence the transport behaviour of the bulk material are screw length and screw design. Decisive for dosing amount are screw diameter, pitch of the screw and, of, course the rotational speed.
In regards to design, the two types are single dosing screws and double dosing screws, and both are available in different designs (geometry). For example, double concave screws are usually designed as two-way versions, single screws are usually single-way. Two-way screws have two spiral coils instead of one, half a gradient apart, on the screw core.
Generally, single screws are very well suited for free-flowing bulk materials. Three well-known designs are spiral screws, augers with core and coil screws, that are equivalent to augers without a core. Spiral screws provide large active transport profiles, have little sticking of product to screw and casing and enable gentle dosing. Coil screws have a large transport profile and thus also great throughput potential. Compared to augers with core, they have a more open design, making spiral and coil screws more suitable for coarser regrind and thicker foil shreds. Additionally, they have less surface for product to stick to and are less susceptible to clogging of the transport profile.
Single augers with core have a smaller active profile. They are particularly suited for dosing granulate. Important here, as for all screw-casing combinations, is to bear the margin between screw and casing in mind. The gap should be approx. three-times the current particle diameter. Otherwise there is the risk of granules getting stuck and jamming the screw.
Double screws are best suited to powders, non-free-flowing and bridge-building bulk materials. While their larger intake areas reduce the risk of bridge-building, it is still sensible to use a dosing device with agitators of a flexible dosing bin with massage rolls (that operate as bridge breakers and screw fillers).
If non-flowing and/or cohesive, sticking powders are being processed, double screws with double concave profiles are an option. Their combing profiles have a self-cleaning effect. Additionally, they prevent uncontrolled leaks of fluidized powders and fine bulk materials. With smaller rotational speeds they also have the smallest amount of pulsation. Double augers are suitable for processing powders and certain fibre preparations.
Finally, if in doubt test the suitability of screw and material combinations beforehand.
Do you need examples of equipment with dosing? Find more information on www.motan.com