54 - What are the advantages of automatic air flow regulation?
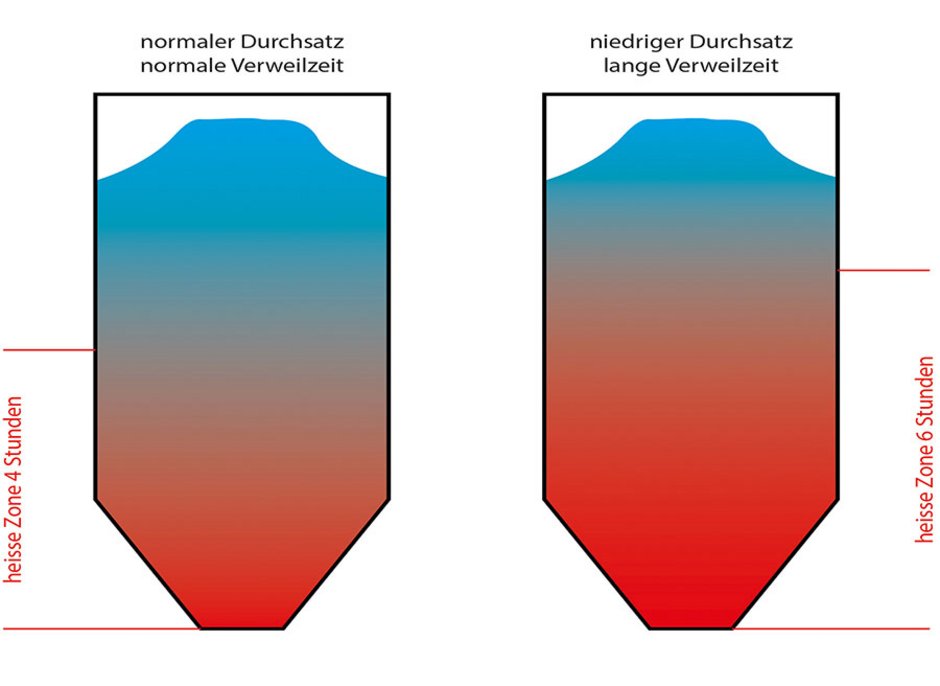
Drying plastics requires a large amount of energy. So, it makes sense to try and find ways of reducing energy consumption where possible – of course, without losing sight of the actual goal: drying material gently to the required processing moisture content.
For dry air dryers, the use of automatic air flow regulation is a good idea and offers a range of advantages. For example, it can adjust energy consumption according to material throughputs. If the material will be sitting in the drying bin for a while, for example during an unplanned production stop, it can help minimise the risk of over drying. And finally, automatic air flow regulation can adjust the drying process to the condition of the material during filling (warm/cold or different moisture contents).
The simplest version of air flow regulation is a dry air generator with a drying bin and a regulated process air blower. The required energy of a drying bin and then also the air flow is calculated by the controls for example according to the throughput, the temperature and the moisture content of the material when filling.
In addition, difference of the return air temperature in comparison with the intake temperature also plays a role in the calculation, as the dry air cools on its way through the material. This is caused on the one hand by the cooling effect of evaporating water, and on the other by the cooling effect of the cold undried material flowing into the drying bin from above. The impact of the return air temperature on the regeneration of the molecular sieve was explained in issue 53.
If multiple drying bins are being supplied by one dry air generator, air flow is regulated automatically by the damper flaps at the air intake of the drying bin. This means that the air flow can be individually regulated for each bin according to actual need. The dry air generator regulated the entire air flow according to the total need of all connected drying bins.
Automatic air flow regulation is helpful and practical for operation for multiple reasons. Start-up time for refilling can be shortened by measuring the return air temperature. For this, the system initially makes the maximum air flow available for the drying bin because of the cold material and relatively high water content. As the temperature of the material increases and the moisture content decreases, the air flow is automatically reduced. After production start the air flow will even out automatically.
During running operation this concept also considers different temperatures and varying moisture content of material intake depending on day/night operation and/or different seasons. Only the actual currently required air flow is provided.
An important aspect in the context of air flow regulation is the energy balance of the drying bin. The principle is based on the energy provided by the air flow is equal to the energy carried off by the material flow (the material taken for processing).
If, for a bin, less energy is carried off (through material extraction) that provided, for example when throughput is reduced, the temperature gradient in the drying bin increases. This means that material gets hotter towards the top and the material intake. Then there is a risk of over drying or thermal damage to the material, because it achieves its target temperature sooner and keeps it for longer.
Reversely, if more energy is carried off than is introduced, the temperature gradient shifts down. The material at the bin outlet does not reach the necessary drying temperature and the required residual moisture content.
How can different equipment put together make the most out of your drying process?
More about drying you can find on www.motan.com