44 - What is to be taken into account with regard to the material discharge?
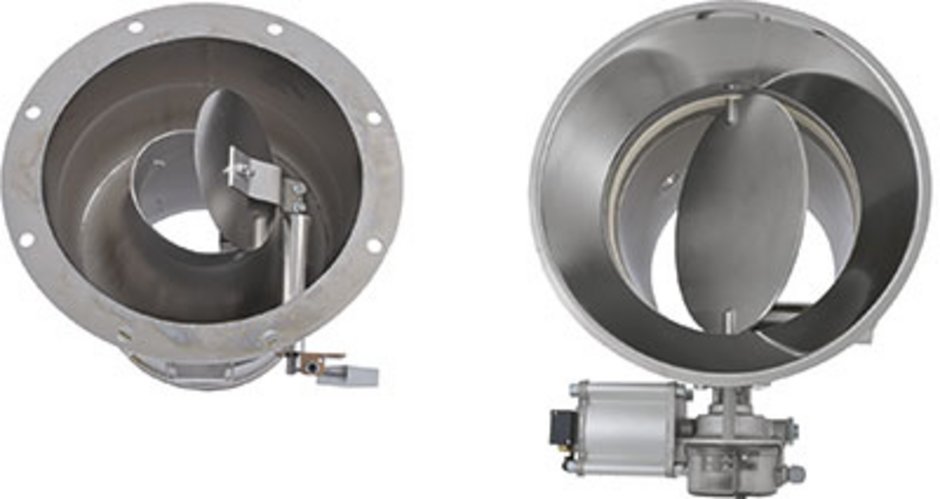
One task of the material supply is to convey material to the hopper loader on the processing machine. It is equally important how the material is transported from the material tank of the hopper loader to the material hopper on the machine or to the dosing unit. The material discharge plays an important role here. Its diameter and the design of the outlet flap depend to a great extent on the flow properties of the material to be conveyed and of course on the required throughput. In the case of highly viscous powders, a larger outlet diameter than for free-flowing granulate is normally required.
In the simplest case, for example for free-flowing granulate, a swivel outlet flap with a counterweight is sufficient, whereby the outlet can also be fitted with a gasket. As soon as there is a vacuum in the hopper loader, the discharge flap is pulled shut and therefore seals the tank. In the ideal case, the flap position (open or closed) is visible from the outside, which helps a fault to be discovered quickly. The counterweight supports the movements of the flap, which remains completely opened in the material after the conveying and discharge process. If the material fill level decreases, the flap swings into its rest position and a switch triggers a requirement message.
Malfunctions of the flap due to granule residue left behind can be remedied with an integrated mechanism. A damper on the stop prevents sudden closing of the flap. In this way, granulate residue left behind can be extracted before it is wedged in by the flap and the vacuum cannot be correctly generated.
For special applications, for example dosing of viscous powders, a large, controlled rotary flap can ensure optimum material discharge. When opening and closing, the rotary valve acts, so to speak, as a discharge element, whereby it simultaneously prevents the formation of bridges. Even when differential dosing is used (loss-in-weight principle, see Episode 9), a controlled, pneumatic or motorised flap may be required, for example if there is no refill unit. In the case of differential dosing, the complete dosing station with the storage bin including its contents and dosing device is weighed and the weight loss due to the material discharged is measured continuously.
If a requirement message is issued – triggered by the fill level sensor in the material hopper of the dosing unit or by the control when the minimum weight is reached – the discharge flap on the hopper loader opens and more material can flow in. At the same time, the dosing system switches from gravimetric to volumetric mode. Then the discharge flap closes and gravimetric mode is resumed.
Another application for controlled flaps is conveying of very light material. This prevents delays in the discharge of the material because the flap does not open completely due to the low weight of the material.
How can flaps look within a system? Find more information on www.motan.com