38 - How do the various vacuum generators differ?
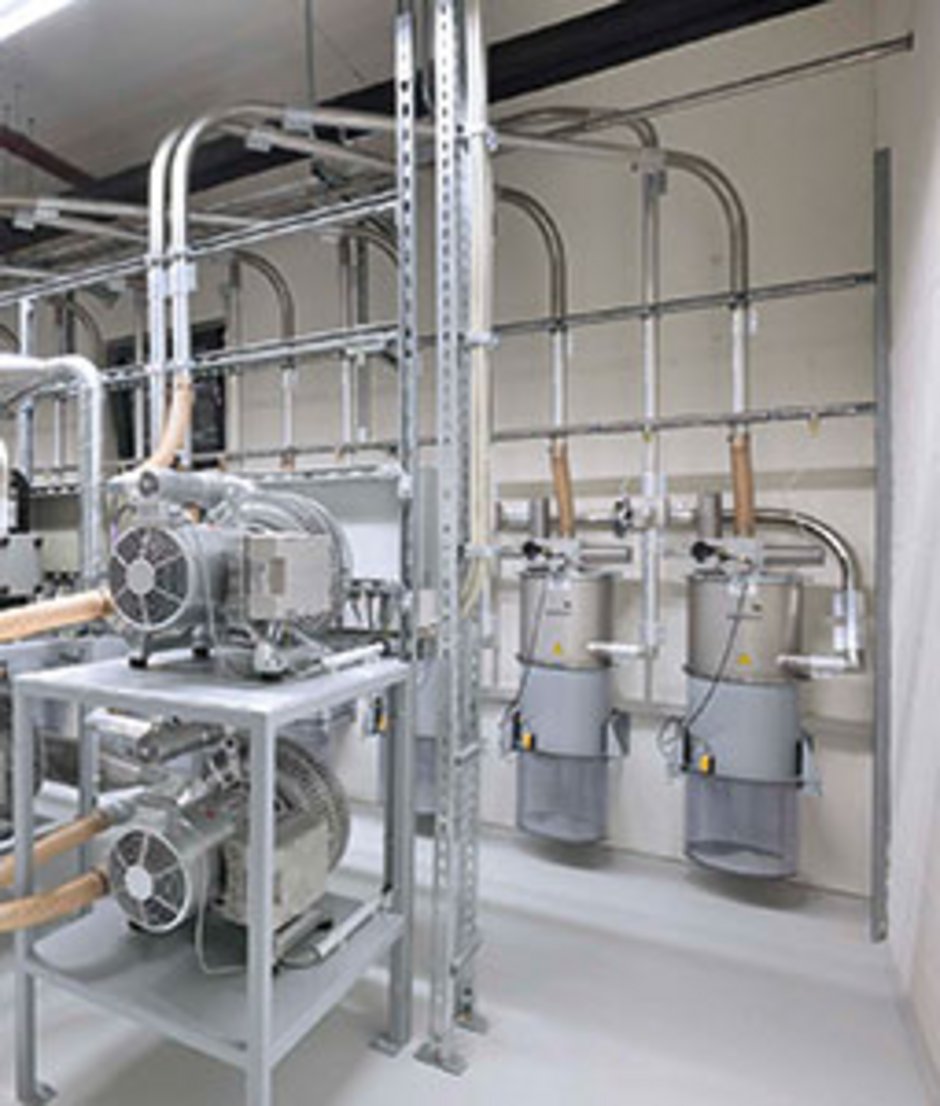
Part of the heavy workers of pneumatic suction conveying – the precise term for the most important conveying method in plastic processing – are without a doubt the vacuum generators.
They must run interference free around the clock if required, should be as maintenance free as possible, and ideally should operate economically and as needed. Simply put, vacuum pumps generate a vacuum in the material hopper on the processing machine. The air that then flows in after transports the granules of powder through the pipe and hose lines into the hopper.
A safety filter installed between the pipe lines and the vacuum pump prevents contaminated air or dust and granule particles damaging the pump. Some of the most important vacuum pumps are:
- Side channel vacuum pumps
- Claw vacuum pumps
- Disc vacuum pumps
- Root or rotary blowers
Side channel blowers are the most common and are mainly used for simple conveying tasks with short distances and large volumes. They operate contactless without oil and therefore require almost no maintenance.
Rotary blowers also operate contactless and without oil. They are suitable for large throughputs at low pressure differences, but this restricts the conveying distance.
Disc or claw pumps are suitable for larger distances. The disc principle for suction conveying operates with circulatory oil lubricant, which requires regular maintenance. As a result, these robust all-rounders are suitable for a large range of applications.
The claw vacuum pumps operate dry and contactless and are considered to be very energy efficient and safe.
The pumps differ particularly in how they operate and thus also their effectiveness. They can only be compared when restricted to the characteristic curve of volume flow based on intake pressure.
When designing a suction conveying system, various criteria need to be taken into consideration when choosing a suitable vacuum generator. As well as the general environmental conditions (for individual cases the height above sea level), the material and its properties, length and diameter of the material lines, and the line system must be considered.
With this data the required pressure difference and volume flow can be determined – and the most suitable vacuum pumps can be selected. Maximum requirements of the units to be supplied with material are crucial for the necessary power of the vacuum generator. In the simplest case this means that the material loader furthest away with the highest throughput determines the power performance.
Standard vacuum generators run with constant performance, regardless of the actual requirements of each material loader. This is why a vacuum generator with power regulation may be beneficial. In combination with the correct controls, power regulation can adjust the power to the actual requirements. As a result, material protecting conveying speeds can be set individually for every material loader, every conveying distance, and every pipe diameter. Energy consumption then also corresponds to the actual requirements.
Vacuum generators within conveying systems? Find out more on www.motan.com