37 - How can abrasion be minimized for vacuum conveying systems?
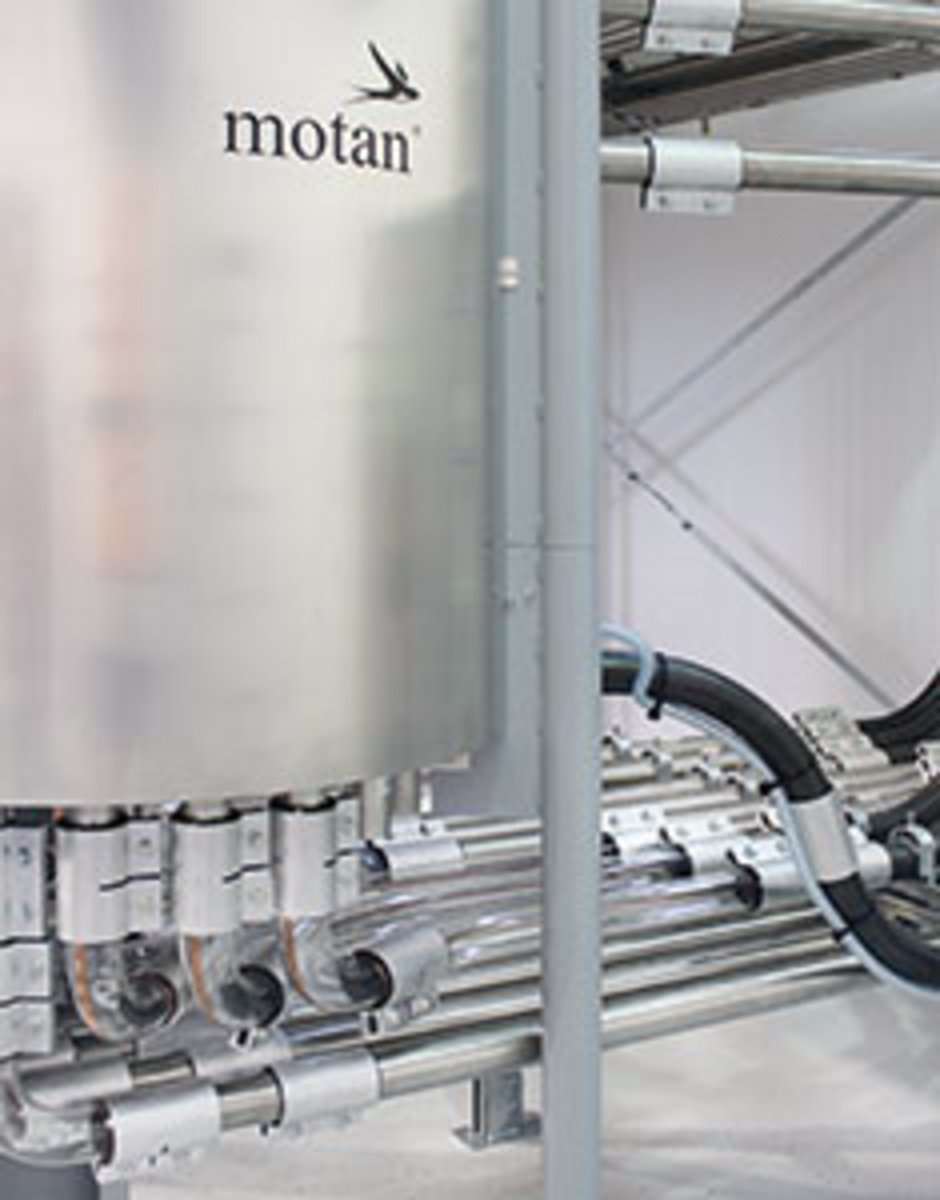
The distances the material travels in the pipe lines from the material supply to the processing machines can be gruelling – both for the material as well as the material lines. The key word here is “abrasion”.
What causes abrasion of the material is usually a combination of mechanical and thermic stress. Particularly at high conveying speeds, there can be lot of contact between the material and the inner walls of the pipes (particularly in pipes) which leads to high amounts of friction. As a result, granules can break, dust can be generated due to abrasion, or the surface can plasticise due to the friction heat.
Plasticisation can lead to strands forming (“angel hair”) or films (“snake skin”) can peel off of deposits. Aside from the fact that material is being lost, these contaminations can lead to interferences with the conveying units up to complete blockages of the material line.
For line systems and material loaders, abrasion due to mechanical stress of the material is the main focus. This is particularly the case when abrasive materials such as glass fibre reinforced plastics need to be conveyed. The pipe bends, material inlet nozzles and flaps of the material loaders, as well as other parts which come into contact with the material, for example at the coupling stations, are affected the most. Undesired effects can be leaks in the conveying system or in serious cases contamination of the end product due to the dust generated by material abrasion.
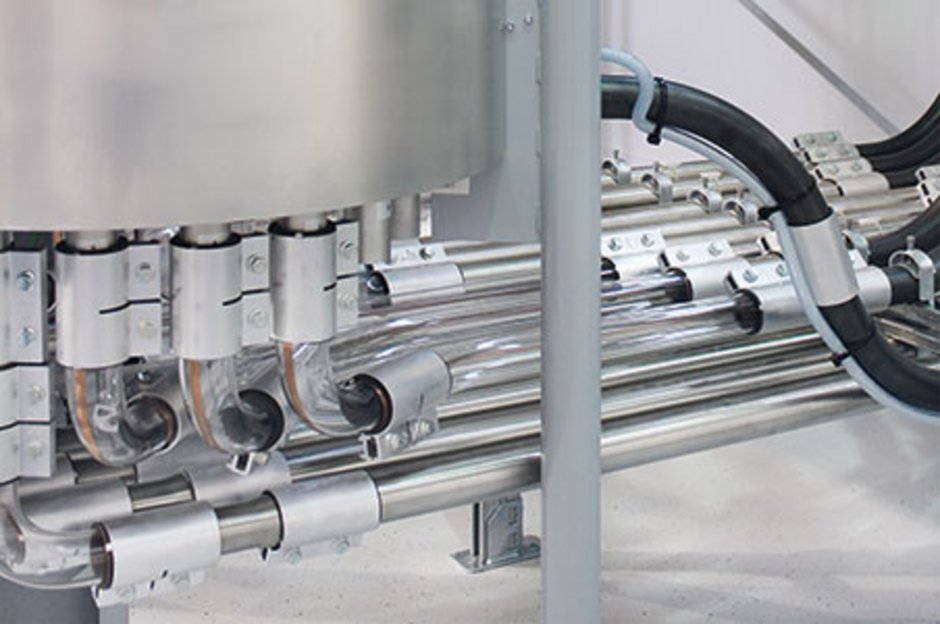
For abrasion protection – or better abrasion reduction – and therefore also material protecting conveying, different measures are possible. Conveying speed has a significant impact. Finding the optimal balance between desired throughput and gentle conveying must already be considered when planning the layout of the system. Conveying distance, the flow properties of the material, the performance of the vacuum generator, and the diameter of the material feed lines are all crucial aspects. It is beneficial to equip material supply with a modern, intelligent conveying system which automatically considers the individual conditions of each connected material loader regarding distance and material.
One of the design features for abrasion protection for the material feed line is most importantly the choice of material. Stainless steel pipes are more expensive, but are far more durable than aluminium. Pipes with shot peened inner surfaces can be used for particularly abrasive material or material which tends to form angel hair. The rough inner surface of the pipes causes the material to be transported turbulently rather than along the inner surface of the pipes. This reduces contact between material and pipe and protects both.
There are different solutions possible for the pipe bends, which are particularly affected. Changes in direction should generally occur in a wide a radius as possible. Asymmetrical bends have also proven to be effective. For abrasive materials and/or high throughputs, bends made from borosilicate glass could be an ideal solution. For particularly difficult situations, special pipe bends are available, for example made from highly wear resistant HVA Niro stainless steel.
Critical areas of the material loaders are the material inlet nozzles and inlet flaps. Reinforced versions are also available here, such as enamelled or glass covered version. For material loaders with a glass body, an angled material inlet can direct the material flow onto the far more wear resistant glass.
You want to see conveying equipment made of stainless steel? Visit www.motan.com