29 - Which marginal conditions are important when choosing a material loader?
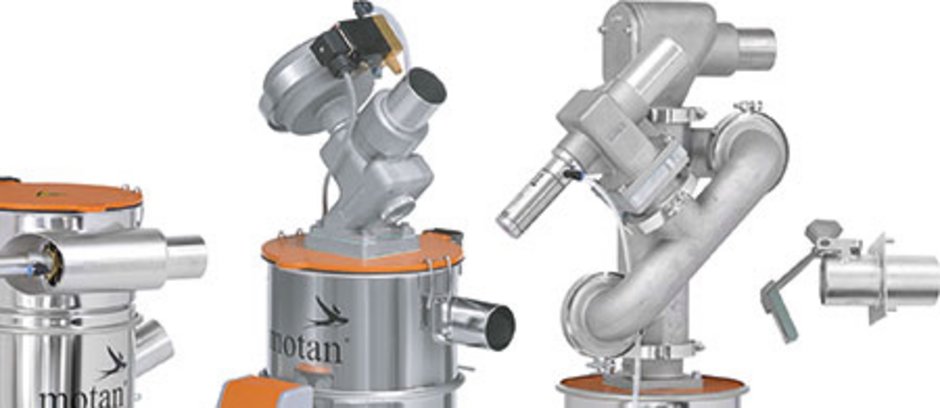
In addition to the throughput and the local conditions, numerous other criteria are important for the conception of a material supply, which can also affect the configuration of material loaders.
This affects the form of delivery and properties of the material to be conveyed. For example, one need to consider whether granulate and pellets, regrind, flakes, or powder is going to be conveyed.
Another deciding factor is whether the material is dusty, whether it tends to form angel hair, or whether it is very abrasive due to its fillers reinforcement materials.
For particular requirements there are specific material loaders, e.g. for regrind with a specific cleaning filter, flake material loaders with particularly large material outlet flaps, or abrasion protected material loaders with reinforced, hardened surface deflectors.
Ideally, a material loader line is set up modularly, in order to adapt to changed production requirements. This applies, for example, to the material inlet pipe as well as the material inlet flap. The material inlet can be fitted to the container either radially straight or angled. A special form is a tangential material inlet in combination with an air outlet with cyclone effect. This is used for fine, dusty material that tends to form angel hair.
The material inlet flap has two important functions: on the one hand, it minimises abrasion, because it functions as a deflector at the material inlet and so protects the filter sieve and casing of the material loader from abrasion. For extremely abrasive materials, an angled material inlet or a glass covered impact plate would be sensible. On the other hand, the inlet flap ensure that multiple material loaders can work together in a system. The moment one material loader of the system starts working, the vacuum in the system causes the flaps of the other material loaders to shut.
For high-grade applications where fine dust must be avoided, the use of a dedusting unit, which is installed directly on to the material loader, is recommended. The then dedusted material can be processed without delay, because the dust is sent to the central filter with the air flow.
High-grade material loaders often have a spring damper at the material outlet, which prevents the flap closing completely when it is not under vacuum. If there are granules on the outlet flap during conveying they will first be sucked away. With increasing vacuum the flap is pushed against the spring and eventually closes completely. This prevents trapped material leading to a loss of vacuum.
Vacuum valves can be installed at the side or on the lid. The side installation has the advantage, that the lid can be opened more easily for cleaning and servicing.
For clean room applications a membrane vacuum which works without pressurised air valve is particularly suited. The required energy is supplied by the vacuum of the conveying system, which opens and closes the valve. Therefore the use this valve is perfectly suited for clean room applications.
You need help with different material loaders? Find a huge range of equipment on www.motan.com