59 - Why and when is a crystalliser needed?
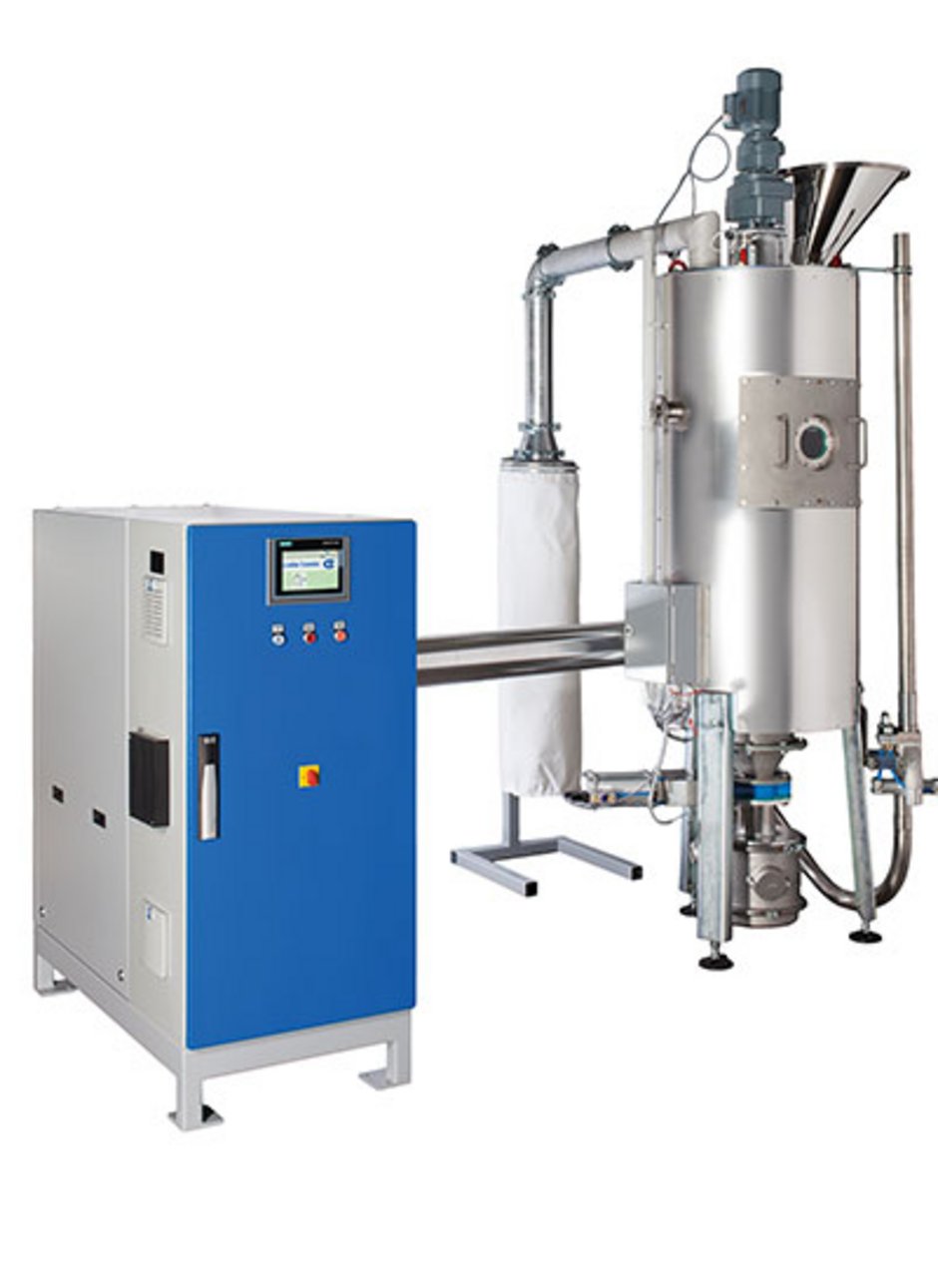
Plastics such as PET (Polyethylenterephtalate), PEN (Polyethylennaphthalate) or PLA (Polylactic Acid) can’t be sufficiently processed unless they have been dried prior to processing. PET, for example, is usually dried at 180 °C to achieve a residual moisture content of under 40 ppm.
After manufacturing, the material structure of PET, PEN and PLA is usually amorphous, as the molten mass cools down very quickly. This amorphous material can be identified by the fact that it is normally transparent. In this context, amorphous means the molecule chains of the material are disordered. On the other hand, the molecule chains of crystallised material are (partially) ordered
When amorphous material reaches a certain temperature (also called glass transition temperature) during the heating process, its state changed from amorphous to crystalline. PET reaches this state at approximately 120-140 °C, way below the required drying temperature.
The problem is that material becomes sticky during the transition from one state to the other and can clump in the drying bin. Once it has a crystalline structure, however, it can be dried to the required temperature with no further problems.
The material is also amorphous for recycling processes, e.g. bottle-to-bottle, or foil stamp residue return, and also needs to be crystallised before it can be processed further.
This is where crystallisers come into play. Crystallisers heat the amorphous material to the glass transition temperature. There are many ways to execute the crystallisation process systematically and precisely. Fixed bet crystallisers prevent clumping using material specific parameters and an agitator, ensuring the crystalline material is correctly conditioned and can flow out properly.
When we talk about crystallised, this usually means partly crystallised. The maximum degree of crystallization of, for example, PET, is approximately 75% with a density of 1.420 g/cm³. The density rises linearly with the degree of crystallisation. The material is sticky at a crystallisation degree of 11% and the density is approximately 1.345g/ cm³. Amorphous PET has a density of approximately 1.335g/ cm³.
The achieved degree of crystallisation is an important value for the crystallisation process and further processing. If it is too low, below the limit where the material is sticky, the material could over bake during subsequent drying. In order to dry PET properly, a crystallization degree of 20 to 30 percent should be the target.
The degree of crystallisation can be determined using various methods, for example using DSC (Differential Scanning Calorimetry) measurement, a density meter or a pycnometer and subsequent calculation.
Do you need an examples for a crystalliser? Find more information on www.motan.com