36 - When is it necessary to purge material lines?
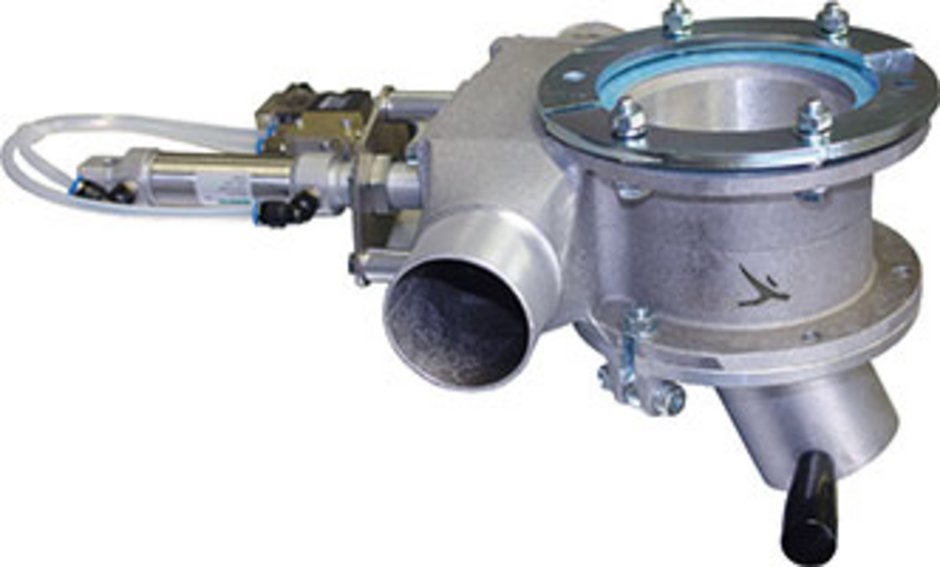
The point of purging is to remove or minimise transported material deposits from a material line. When the vacuum of vacuum conveying systems shuts off after the conveying cycle, any remaining material in the line remains in the line and ideally is transported again during the next conveying cycle.
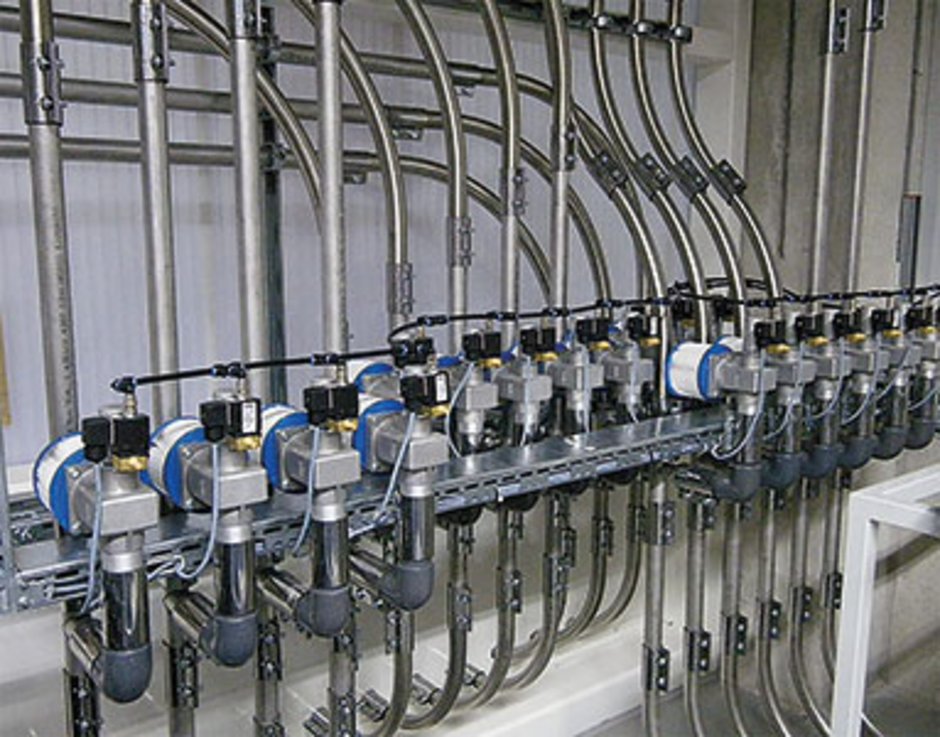
Due to many different reasons it could, however, be sensible or even necessary to purge the material line(s). The term “purging” is very general and does not always necessarily mean that all the material is removed from the material lines. In many cases it is enough to just “free up” the lines.
It is self-evident that complete purging is necessary before a material change to prevent mixing and therefore also waste or worse. The same is true when different delivery points are supplied by the same material feed line from different supply points. This is the case for some automated coupling stations, for example.
In addition, purging can be beneficial when processing pre-dried material, as it prevents material deposits from reabsorbing moisture in the material feed lines.
As a preventative measure against blockages, purging removes any deposits, which is particularly important when processing adhesive materials. The most critical points in the material lines in this case are the bends, as the material can rub against the inside of the pipes and adhere to them.
Even if the material is being conveyed over larger distances of vertically installed pipes, purging can help prevent any blockages occurring at the foot of these line segments. When switching off the conveying stream, any material left in the material lines will fall to the bottom of the bend due to gravity. This can result in problems creating vacuum for the next conveying cycle.
In order to purge a material line, the installation of a purging valve or a controlled suction box is necessary. In order to clear the line, it is often sufficient to let air stream into the line via a bypass opening. To completely purge the material line, a controlled suction box or a two-way purging valve is usually used, which interrupts the material flow and simultaneously opens the bypass. Whether a material line is completely purged or just cleared also depends on the purging time. In is important to bear in mind that extremely long purging times can influence the throughput of the conveying system.
For vertical line segments, in may be sensible to install a purging valve at the foot, in order to completely purge the line.
Depending on the individual situation, it is always important to keep an eye on the possible amount of material in the lines and the volume of the material container at the processing machine.
You need help with your conveying system? Visit www.motan.com for more information.