31 - How does the dedusting of granulate work?
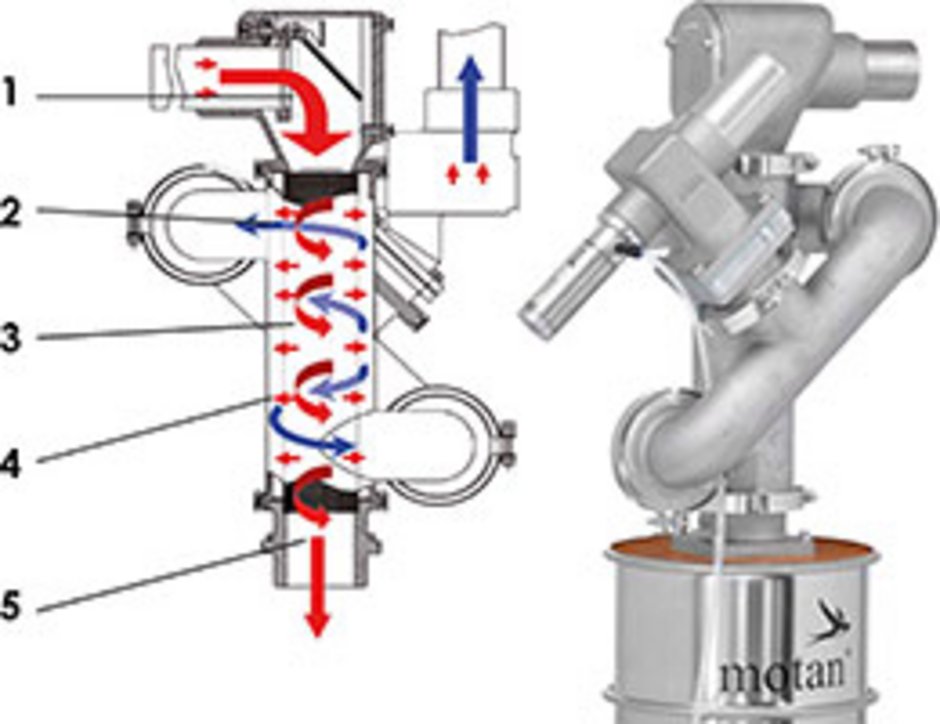
For the production of high quality parts, fine dedusting of the material may be required at the end of the conveying process, even if the material is virgin material.
A so-called inline dedusting unit on the machine with a dedusting attachment installed on the material loader is advisable in this case. The material is dedusted while it is being conveyed in the material loader.
When the granulate enters the dedusting module the material speed (1) is reduced due to the larger cross section at the inlet. The granulate then falls through a perforated pipe (3). The vacuum air circulates around this pipe, causing the material to move circulate in a cyclone-like movement (2). This separated the granulate from the dust particles, which are then sucked away through the perforated pipe (4). The dedusted material falls into the material loader (5), while the dust particles are conveyed via the vacuum output to the central filter before the vacuum pump.
An alternative version is a material loader without filters. Here, the material containing dust is decelerated with an integrated reflector. The material falls due to gravity into the precipitator, while the dust is sucked up by the air flow and is also collected in the central filter.
The central filter protects the vacuum pump. Regular cleaning is important here, the same as with all filters. Automated implosion purging is common, because neither air nor dust is released into the environment. The central filter is connected to the vacuum pump via the air outlet. The dusty air is sucked in from the material feed lines and the material loaders via the air inlet. The tangentially arranged inlet creates a cyclone effect, which already separates some of the dust particles that then fall into the dust collection bin. The filter cartridge separates the remaining dust from the vacuum air before it leaves the central filter.
In order to clean the filter cartridge, the material inlet valve of the central filter closes. This causes vacuum to build up in the filter. Next, a bypass valve is opened, so that air from the environment enters abruptly, causing an implosion that cleans the filter. This cleaning process normally occurs after every conveying cycle.
Central filters are often equipped with pressure control. This measures the pressure difference between air inlet and air outlet and therefore monitors the state of the filter cartridge.
How does a dedusting unit on the machine look like? Find out on www.motan.com