27 - How does the material reach the processing machine?
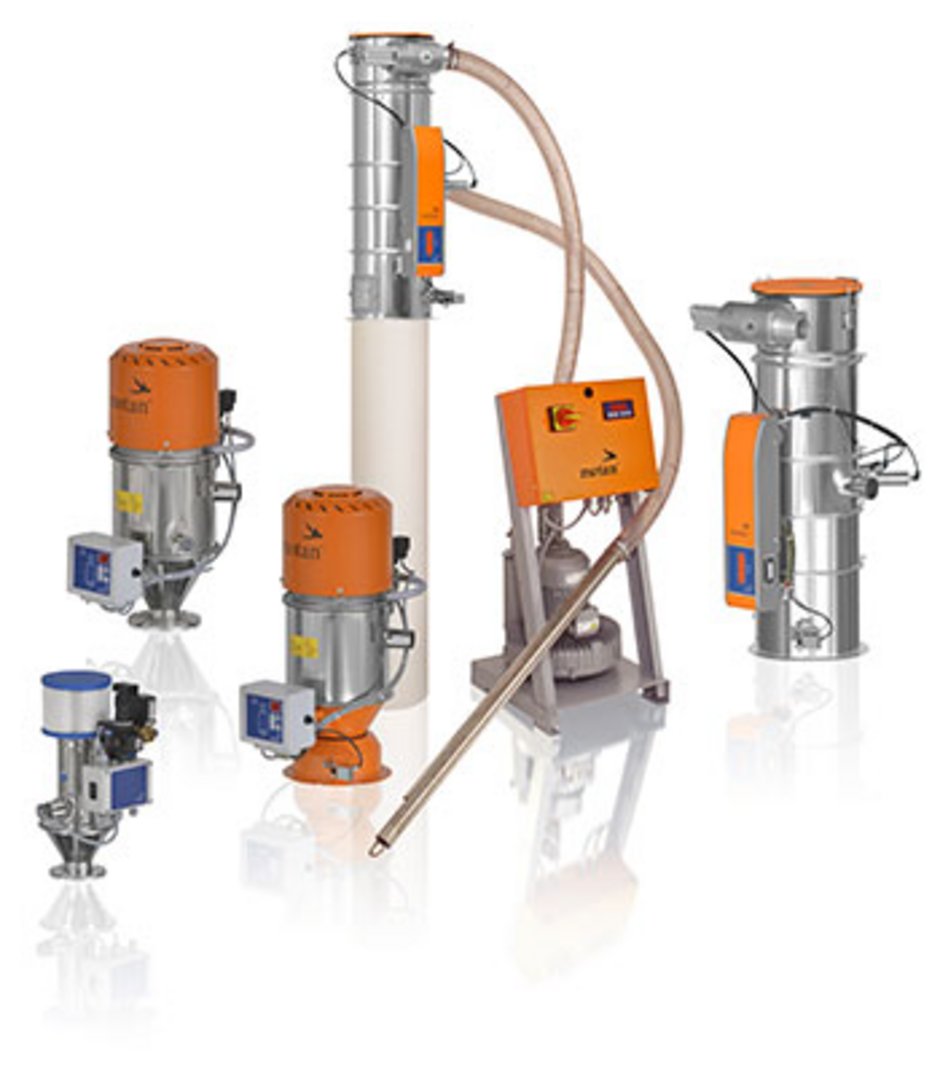
Vacuum conveying, or suction conveying, has established itself in plastics processing as the method of supplying machines with material. Although pressure conveying systems can bridge very long conveying distances, the material supply is disproportionately more difficult compared to vacuum conveying systems. Even the distribution of the material from one discharge point to multiple devices is considerably more complex. Therefore, pressure conveying is used almost solely for the filling of silos.
Vacuum conveying – whether single devices or multiple device systems- is, on the other hand, substantially more flexible. Single devices convey from one discharge point (material storage box) to one receiving device (processing machine, dosing and mixing unit, or dryer). Multiple device systems supply, depending on the concept, multiple receiving devices with material from one or more discharge points.
The basic principle of vacuum conveying can be compared to that of a vacuum cleaner. In the simplest cases, a single device with an integrated vacuum motor – mounted on the machine inlet, hopper loader, or a dosing unit, depending on the design – is sufficient. The following are also part of the standard equipment: A suction hose with suction probe through which the material is sucked from the storage box into the material loader, a dust filter to protect the environment and the motor, as well as controls. Large stand-alone material loaders with conveying capacities of several hundred kg/h of material are operated with a separate blower station which is connected to the material loader via a vacuum line.
Material requests are usually transmitted from a sensor or a fill-level probe tot he controls which start the conveying cycle. The vacuum motor or blower station is switched on a sucks the material. The duration of the conveying cycle can be controlled either by a specific time period of fill level. In the material loader the material is separated from the vacuum air fluidically and is then available form processing. (mo will explain this in more detail in the upcoming issues)
There are different concepts for cleaning the filter. In the simplest case the dust filter is cleaned every conveying cycle automatically with a few blasts of pressurized air. Other concepts equip the material loader with a vacuum valve and an implosion valve for filter cleaning.
You need more information on these different versions of stand-alone material loaders? You can find them on www.motan.com