25 - Which types of material conveying are relevant for plastics processing?
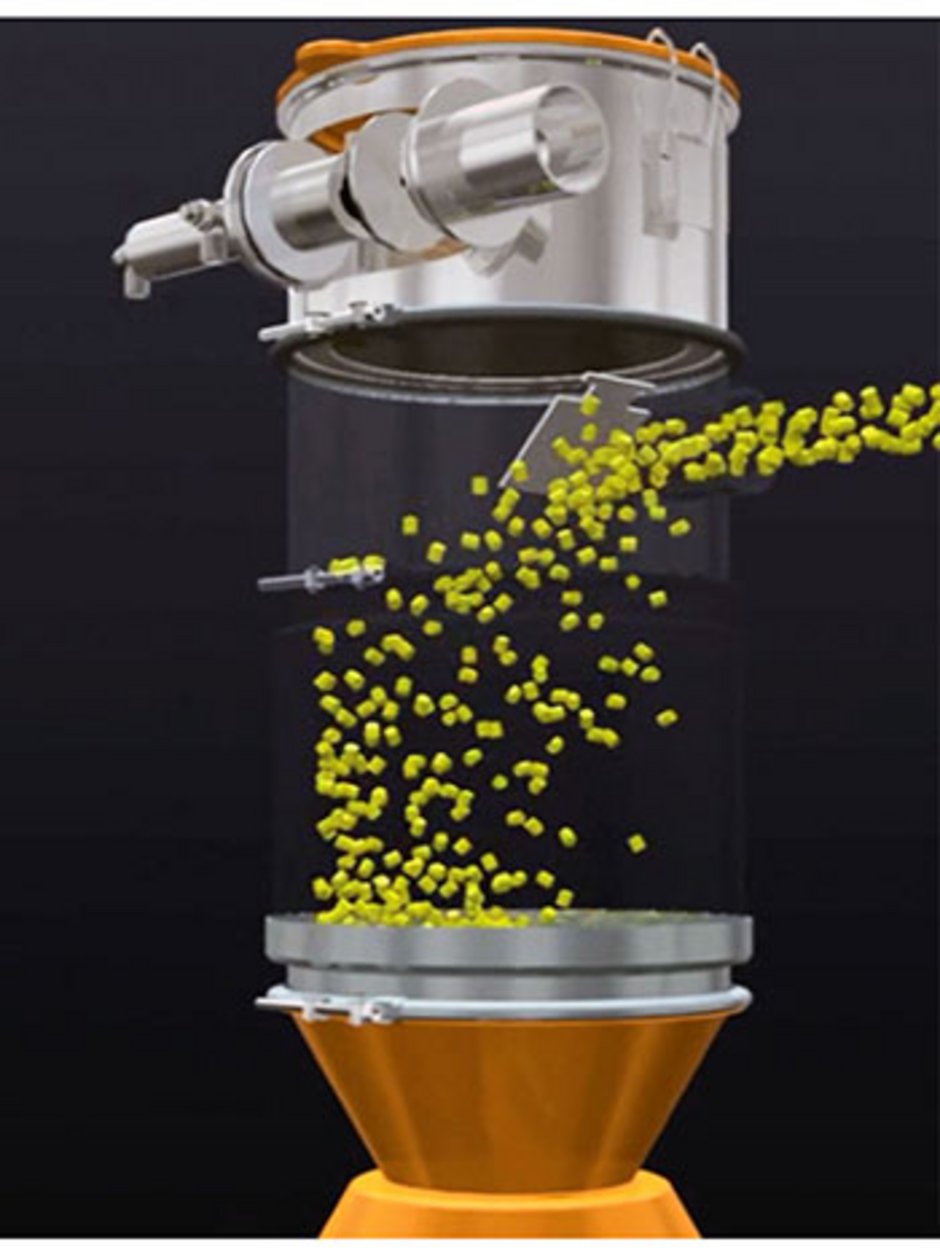
Hydraulic, mechanical, and pneumatic conveying systems are options for material handling in the plastics industry, in regards to the conveying of bulk material. Mo’s Corner will deal with material supply of processing units in particular with bulk material such as granulate, pellets, powder, regrind, flakes, or fibres. Supply systems for injection moulding inserts will therefore not be taken into consideration.
Hydraulic conveying is often used in conjunction with an underwater granulate system in material production and material preparation. Here, granulate is transported by water in open or closed channels, or pipes. After transporting, the conveying medium water, which circulates in a recirculation system, needs to be separated from the material and the material must be dried.
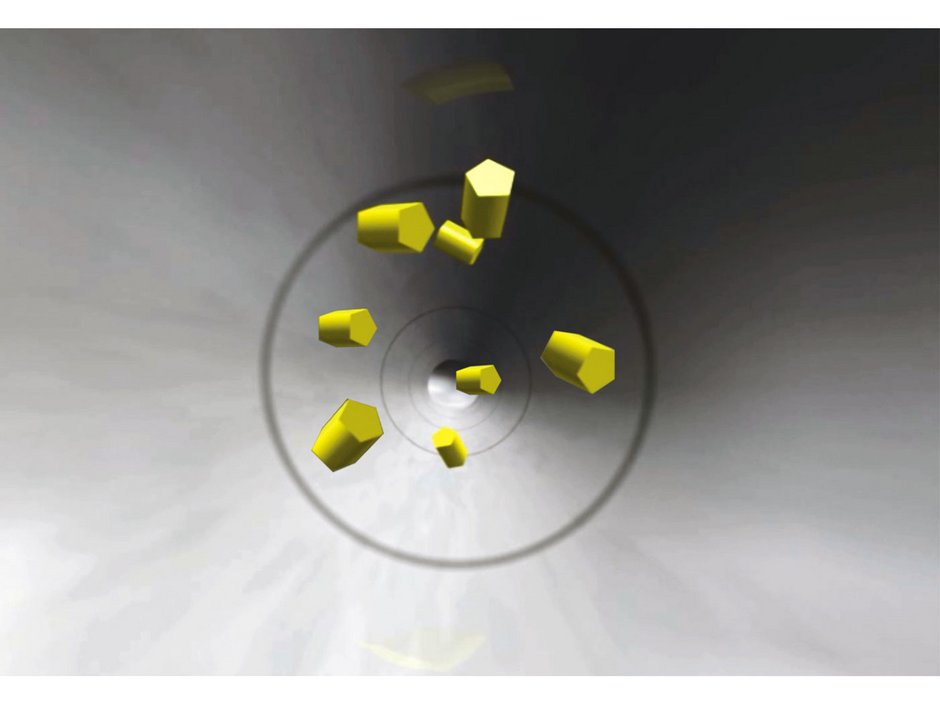
Mechanical conveying systems such as conveyor belts or chain trough conveyors are less relevant for material supply in plastics processing. Flexible augers that consist of a flexible hose with a conveying screw inside which convey dry, free-flowing powder or granulate are an exception to this. Conveying distances of up to 50 m horizontally and 20 m vertically with a bending radius of up to 2.50 m can be achieved with this principle.
The most important conveying principle by far in plastics processing is pneumatic conveying. Just like its hydraulic counterpart, it works according to the so called two-phase current principle. In this case, however, the material is transported through the material feedline with air. The material transport can take place with positive pressure via pressurised air (pressure conveying), or negative pressure (suction conveying with vacuum). The energy transfer between the air flow and the material occurs via the relative speed.
Different conveying states can be differentiated according to material, conveying medium, and material feedline and its geometry. In our case the most important states are dilute phase conveying, strand conveying, and plug conveying. In dilute phase conveying, the particles “float” through the feedline. The material is conveyed with relatively large amounts of air (air flow speed 15-40 m/s; particle speed 10-25 m/s) und low pressure. The air load, or the ratio of material to air, is less than 10 kgmat/kgair.
Strand and plug conveying are also called dense phase conveying. With strand conveying the air (speed 10-20 m/s) pushes part of the material as a strand across the bottom of the feedline while another part floats above. The air load is between 20 and 40 kgmat/kgair. With plug conveying the accumulated material (clusters, dunes, or plugs) is pushed by the air slowly but with high pressure through the material feedline.
Dilute phase and strand conveying can take place both in pressure and suction operation, plug conveying, on the other hand, only in pressure operation.
How can equipment for different conveying processes look like? You will find more information on this topic here: www.motan.com