07 - How do volumetric synchronous dosing units work?
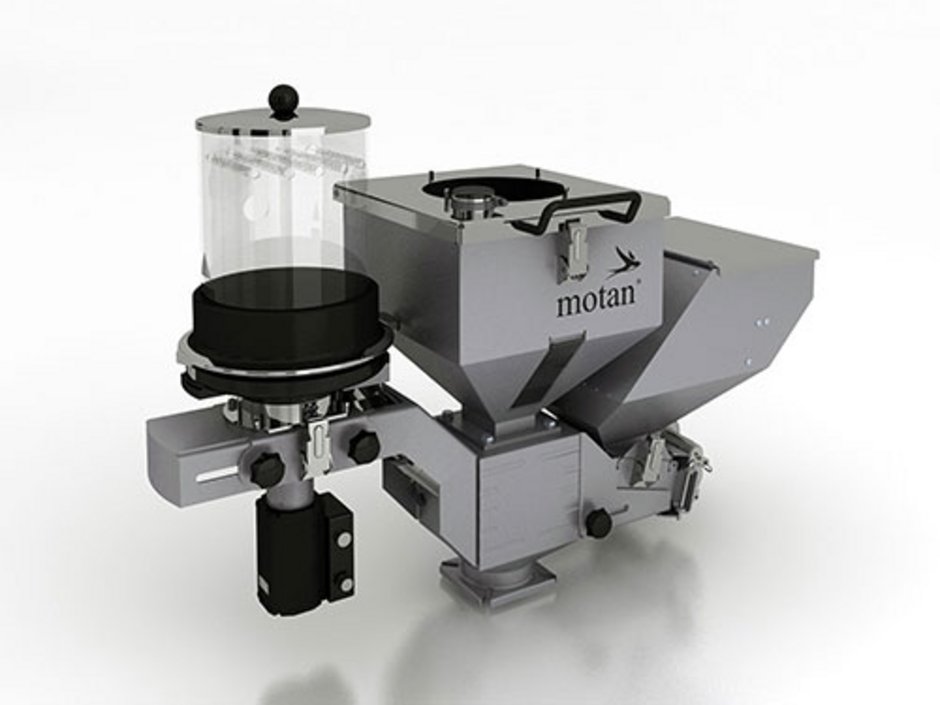
Synchronous dosing stations meter all ingredients simultaneously. The mass flow corresponds to the recipe at all times, and the dosing cycle and mass of material metered is synchronized with the material feed on the downstream production system. The dosing stations’ control system ensures that the right amount of each ingredient is metered, on the basis of calibrated values and in the ratios required by the recipe. The material is fed directly into the feed throat of the processing machine; it is not necessary to actively mix the components.
For synchronous dosing, there are two possible unit configurations:
One option is to meter all components, much like in asynchronous volumetric systems. For the most part, the dosing equipment is controlled independently of the processing machine. The dosing cycle is initiated and halted by a signal emitted from a probe in the feeder tube, positioned directly above the feed throat of the machine.
Alternatively, you can meter all materials except the main component. The main component flows continuously into the throat of the processing machine, while the other additives are fed from the respective dosing modules.
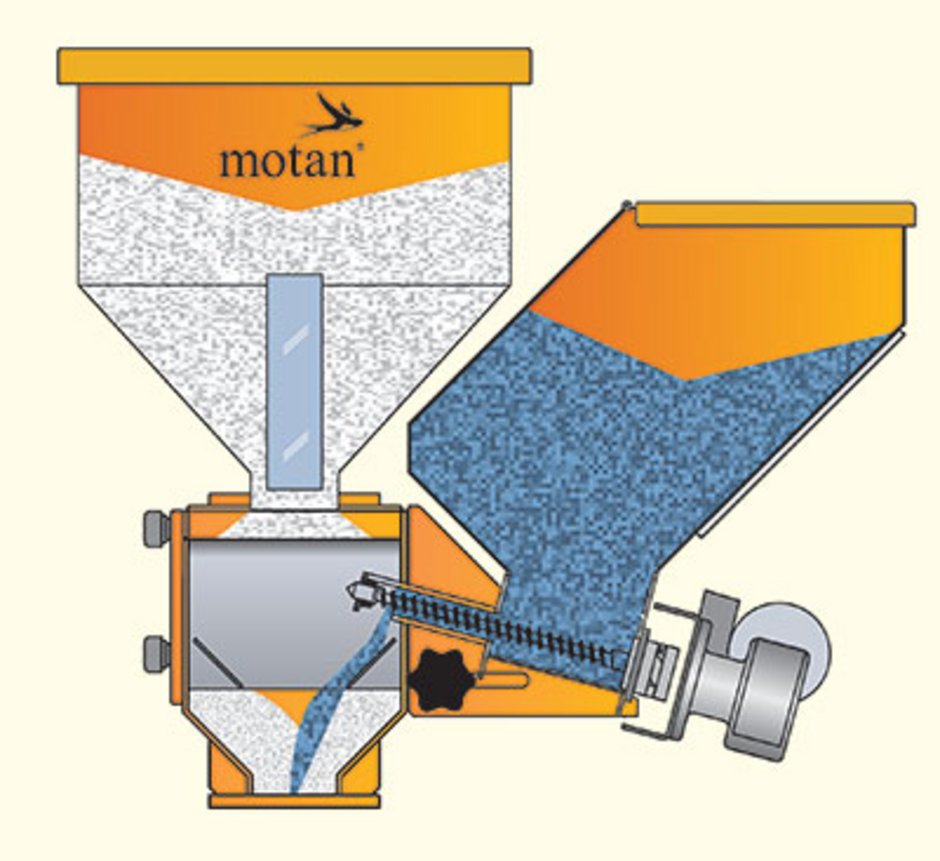
With injection moulding, the mass flow is constant during the screw phase of the moulding machine. The system’s control unit calculates the speed and cycle of the dosing modules on the basis of shot-weight, additive ratios and calibrated values. The injection moulding machine gives a signal to start the dosing cycle. Modern control units respond to changes in the screw back time, and automatically adjust throughput and dosing cycle as necessary.
Whatever type of synchronous dosing unit you are using, the dosing modules must be capable of metering the required mass flow while the material is being fed (screw back time). Because injection moulding is a cyclical process, the relative flow rate is far higher than the absolute flow rate per hour.
You want to have an example for a synchronous dosing unit? You can find it on www.motan.com