04 - How do various types of dosing device work (2)?
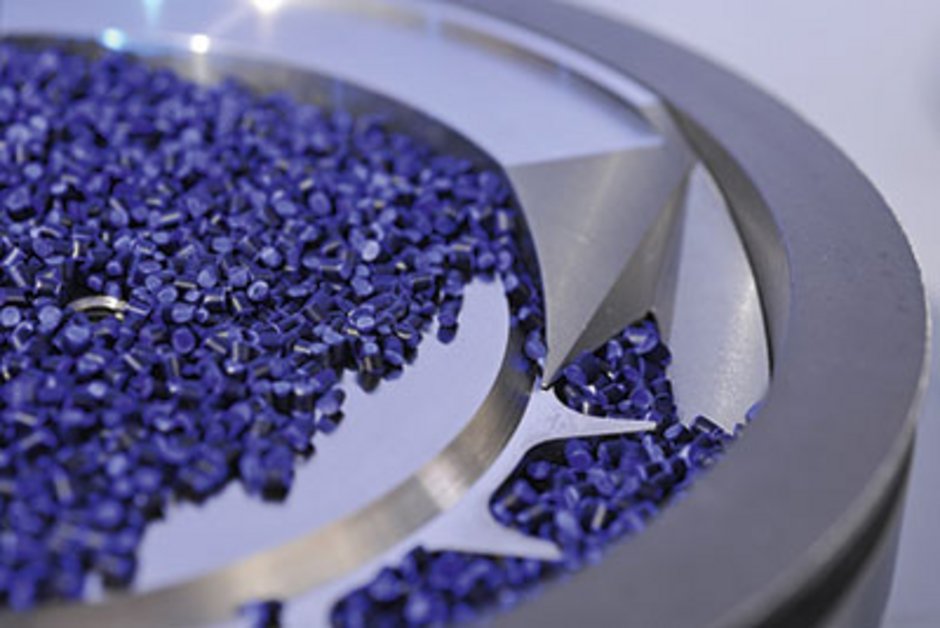
In the last article (3), we talked about dosing screws and cone valves. Now, let’s take a look at some other widely used dosing devices:
- Slide-gate valves
- Disc dosing elements
- Rotary valves
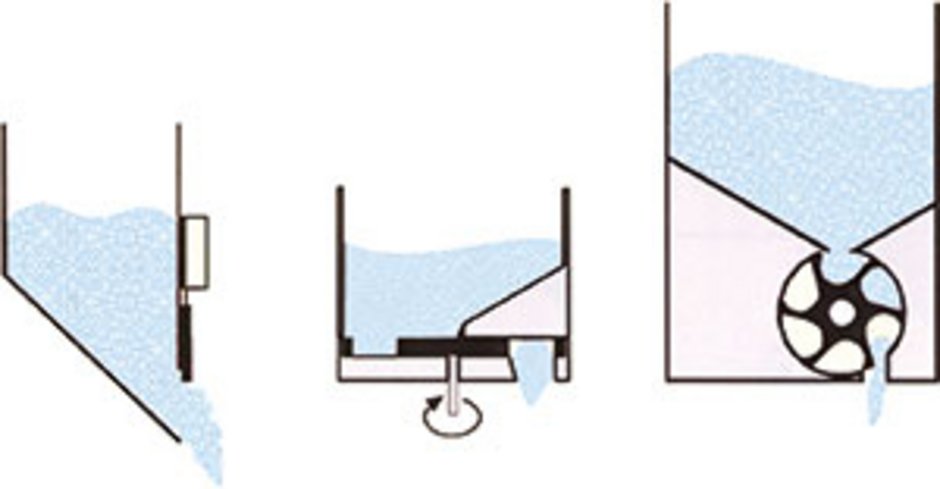
Like a cone valve, a slide-gate valve is a passive system – i.e. the material simply flows out of the supply hopper. Output is controlled by the slide, which can be positioned either vertically or horizontally. Material can be metered continuously or in batches and the volume dosed each time will depend on the cross-sectional area of the slide and how long the valve is open.
Slide-gate valves are suitable for granular and free-flowing powders. If working with materials that do not flow well, on the other hand, you run the risk of the material sticking or clumping together (often called “bridging”). To avoid this, an additional device that positively feeds the material is necessary. Slide-gate valves can be used for smaller and larger material throughputs; however, they are only suitable for gravimetric batch dosing systems. Synchronous operation is not possible, making a downstream mixer a must.
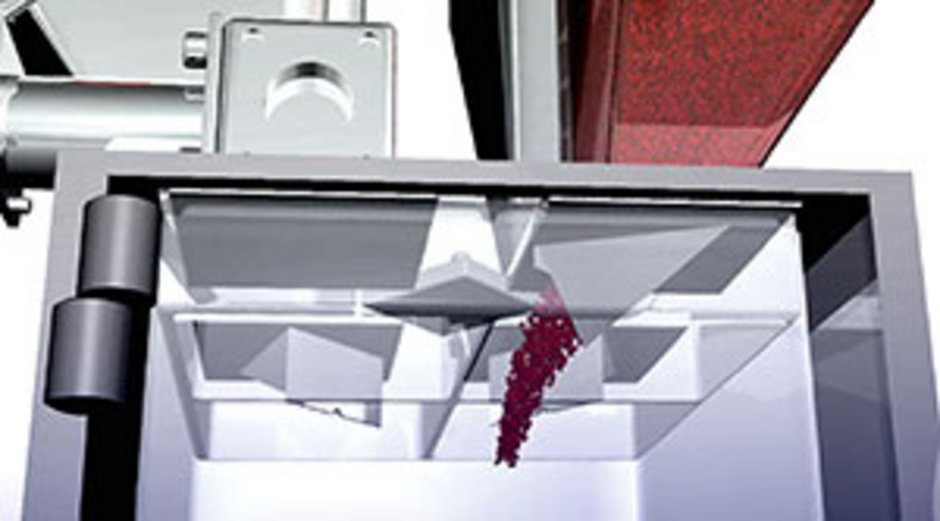
The disc dosing unit and the rotary valve are based on the same concept: they actively meter the material by enclosing the required volume in chambers – similar to measuring using a cup or tablespoon when cooking. And just like in the kitchen, any excess material is “leveled off” before dosing. This method is also known as “digital-volumetric”, because when the technology was in its infancy (or in the case of very simple systems); the only way to create discrete volumetric units was to use entire chambers. Depending on the design, today’s systems are capable of far greater precision. And you can achieve even more precise measurements by adjusting the dosing device to the required throughput.
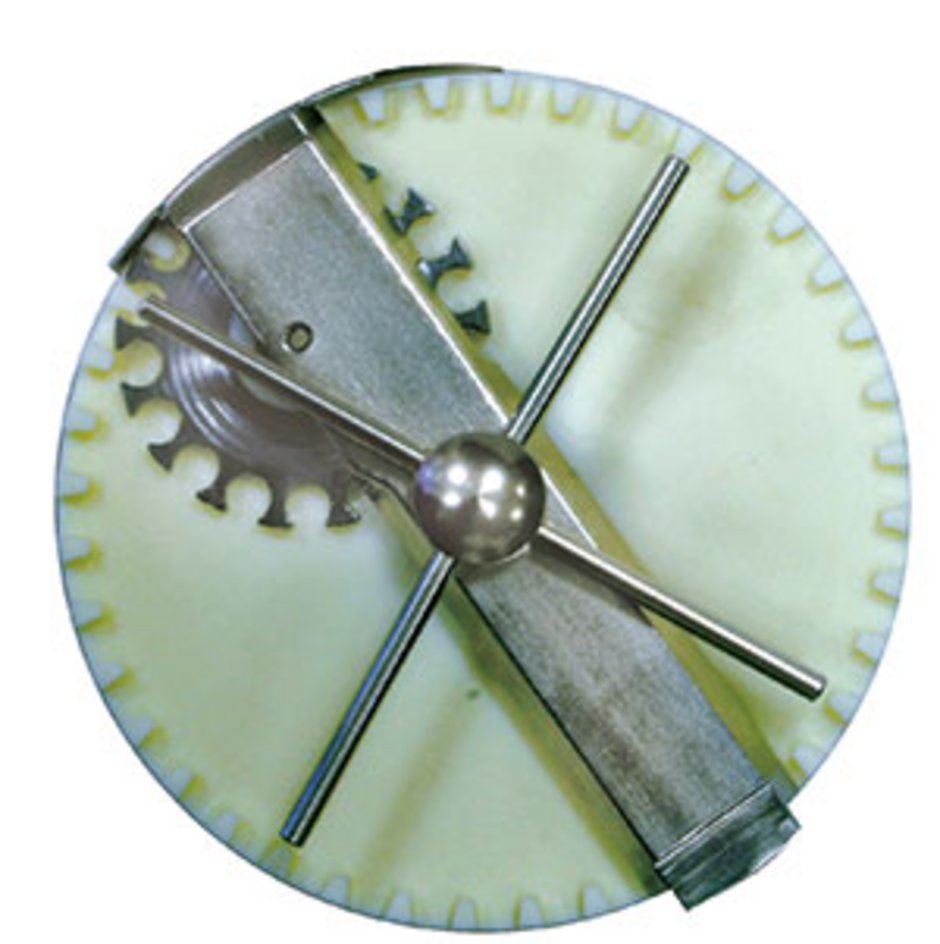
Both the disc dosing unit and the rotary valve can meter material continuously or in batches. The volume dosed in a given period of time depends on the volume of the chamber and the rotary speed of the wheel. Both devices can process granular and free-flowing powders, and are suited to dosing very small to medium material throughputs. If you are using material that does not flow well, you will need additional equipment to positively feed the material. This allows you to ensure each chamber is filled to the same degree. Both dosing elements are deployed primarily in volumetric systems.
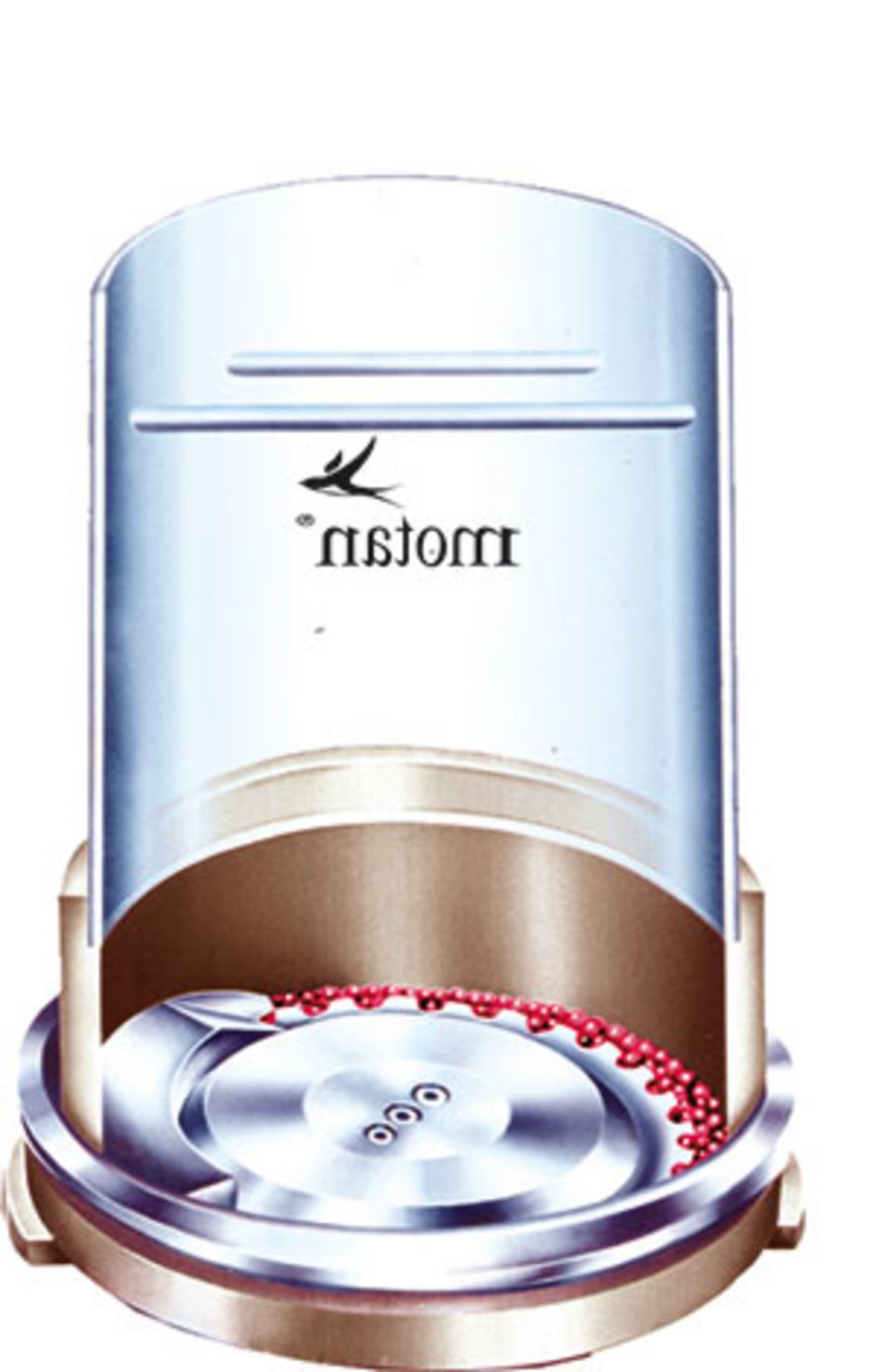
A variety of disc elements and rotary valves are available for processing a range of throughputs and materials. In addition, disc dosing units can be fitted with a blade for leveling off excess material. This can cut granules if required, ensuring each chamber is filled correctly and enhancing the consistency of the volume. This type of disc dosing device is particularly suitable for small volumes of micro-granulate.
You want to learn how different dosing devices can be used with equipment? Visit www.motan.com