03 - How do the various types of dosing devices work (1)?
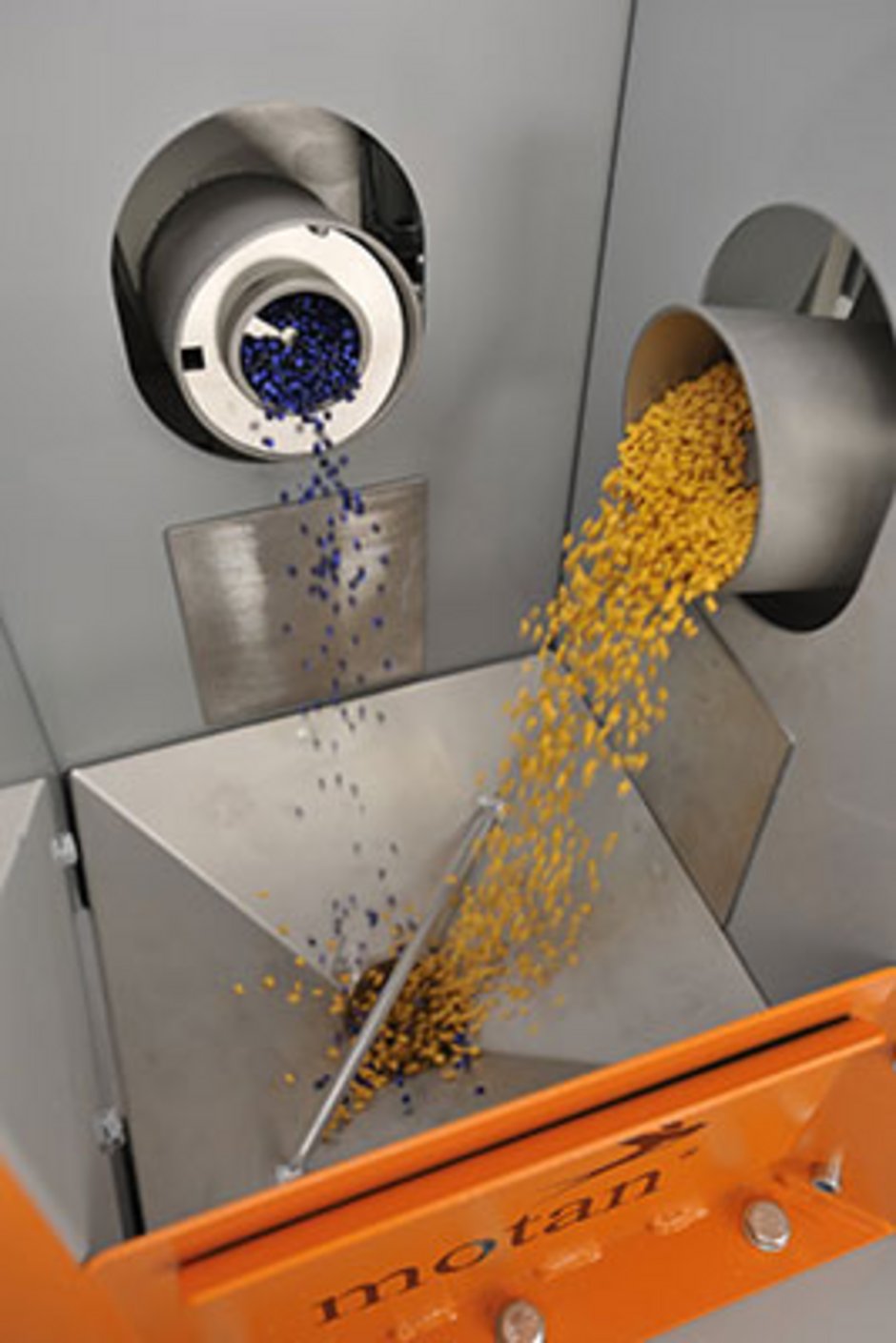
To choose the right dosing device for your application, you need to consider three key points: what are the properties of the materials you are working with; which method will you be using (volumetric or gravimetric); and what volume per cycle or per unit of time will you be processing (flow rate). Plus, the surrounding environment (vibrations, clean room conditions, etc.) plays an important role.
The most common dosing devices used in injection moulding are:
- Dosing screw
- Cone valve
- Slide-gate valve
- Disc dosing device
- Rotary valve, rotary wheel or roller
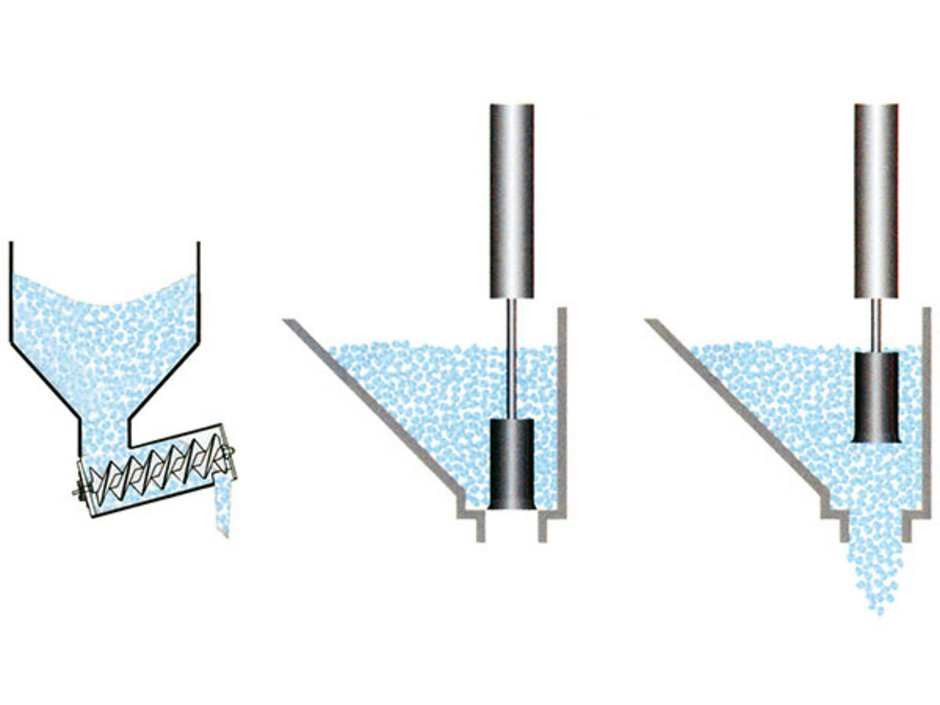
Dosing screws actively meter material using a spindle (screw) and simultaneously convey it to the point of discharge. The screw is encased in a tube (dosing sleeve). The amount of material dosed will depend on the diameter and pitch of the screw, and how fast the screw rotates. To prevent material accidentally falling out, dosing screws are often set at an upward incline – which has the added benefit of making cleaning easier.
The output from a dosing screw is continuous. This widely used device is available in various designs for a range of materials – and is suitable for both volumetric and gravimetric systems, and large and small material throughputs.

When working with non-free-flowing materials, you need an additional device such as an agitator to positively feed the ingredients. Friction between the screw and the tube can generate heat, which can create problems if the material has a very low melting point. An advantage of the device, on the other hand, is that it allows for synchronous operation – making subsequent mixing unnecessary.
In contrast, the cone valve is a passive system, i.e. the material simply flows from the supply hopper. A valve (created by the cone and a cylinder) regulates the flow. The material can be metered out either continuously or in batches.
The amount of material dosed depends on the cross-sectional area of the cone, the stroke length of the cylinder, and for how long the valve is open.
Because the piston moves up and down vertically, the cone valve is suitable for a range of materials – free-flowing, non-free-flowing, and even those that tend to stick or clump together. If you are using non-free-flowing materials, however, additional equipment will be necessary to positively feed the material. Cone valves are mainly used in gravimetric batch systems and are suitable for throughputs of all sizes. However, because this method is not compatible with synchronous operation, a downstream mixer is necessary.
Next time, mo will explain how the other types of dosing device work.
You want to learn how different dosing devices can be used with equipment? Visit www.motan.com