motan innovation award mia awarded
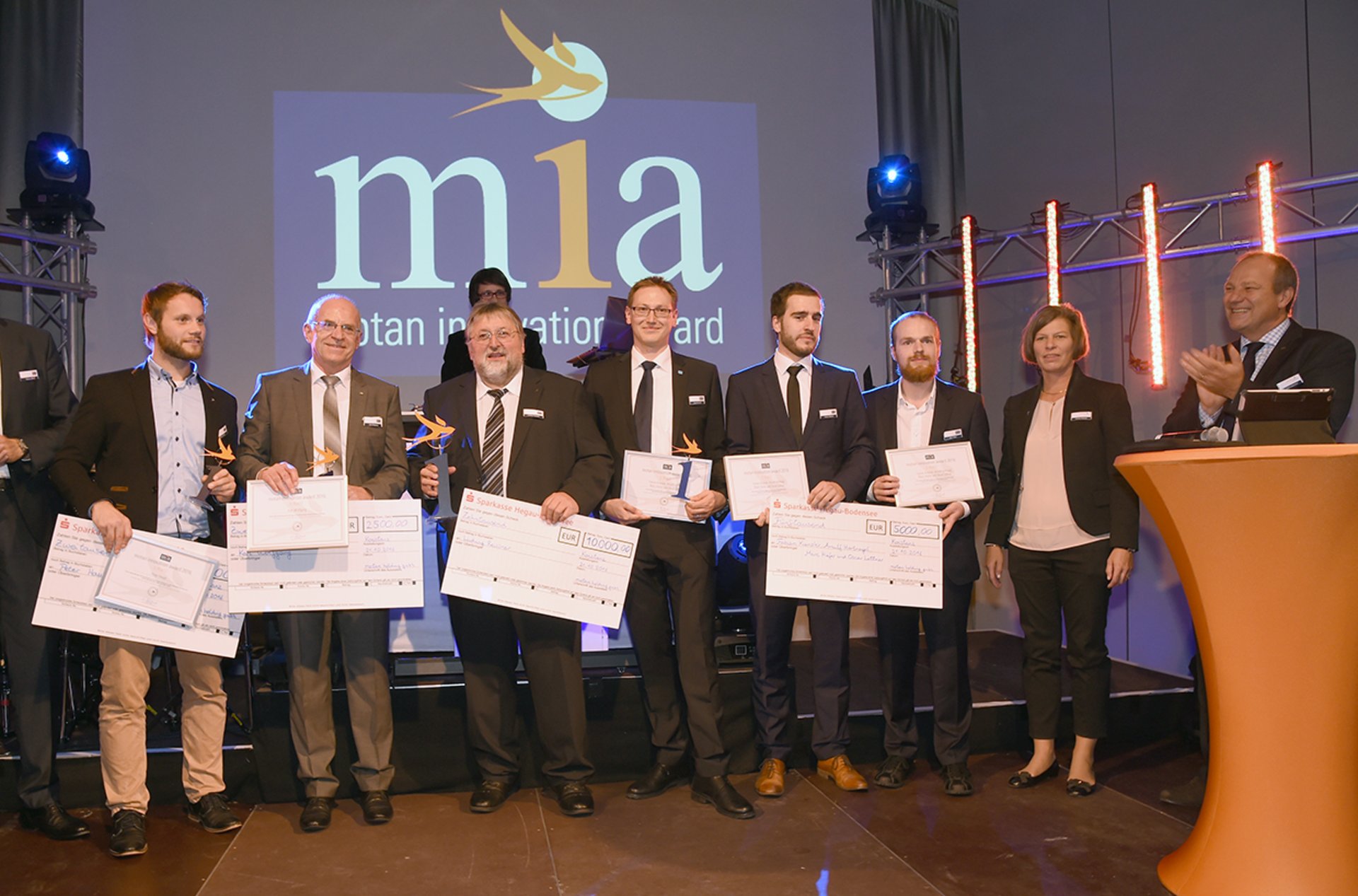
The excited waiting has come to an end: On the 21st October 2016, motan announced and honoured the winners if the competition mia – motan innovation award 2016 – which began roughly 10 months ago.
A top-class jury evaluated in advance the nominated solutions intensively and detailed in regards to level of innovation, relevance for practical application in the plastics industry, and feasibility and market potential within material handling. Instead of the usual three, four innovations for different functions of material logistics and handling have made it onto the podium: Along with first and second place, the jury awarded two third places. Prize money of over 20,000 euro was donated by motan holding.
1st place: Ludwig Reissner
With the Matrixkoppler, an automated material station for small conveying systems, Ludwig Reissner has made material changes even more efficient and safe. Conventional material stations require manual switching of the hoses leading to the material loaders during material changes. The Matrixkoppler automated the material allocation with a newly designed multiple switch. This way, contamination from neighbouring lines can be prevented. This is practical, cheap, and completely new.
motan is honouring this development with prize money of 10,000 euro.
2nd place: Team Fabian Kienzler
Together with Arnulf Hörtnagl, Marc Hiefer, and Oscar Lattner, Fabian Kienzler has developed an alternative method for drying of granules. At the core of the innovation is the use of an inductive heating element – for energy transfer via radiation. Here, pre-warmed air flows through the granules to extract moisture. This new automated drying is efficient and can be controlled precisely. This idea was born out of the search for a dew point sensor.
motan is honouring this development with prize money of 5,000 euro.
3rd place: Peter Haupt
Energy which is used for drying and dosing in usual material flow constellations, is used more than once by the dry dosing unit developed by Peter Haupt. The idea is focussed on dramatically reducing energy consumption – and therefore costs. Operation can then also be designed more ergonomically.
motan is honouring this development with prize money of 2,500 euro.
3rd place: Karl Wolfgang
Better utilisation of material and increased cleanliness are the benefits of using the Octa-Flow-Bag by Karl Wolfgang. If octabins are emptied with an automated conveying system in production, then material normally remains in the corners and must be sucked out manually. This new development transports remaining material automatically into the middle of the octabin, where it can be removed easily.
motan is honouring this development with prize money of 2,500 euro.