55 - ¿Se puede ahorrar energía con el control automático del caudal de aire?
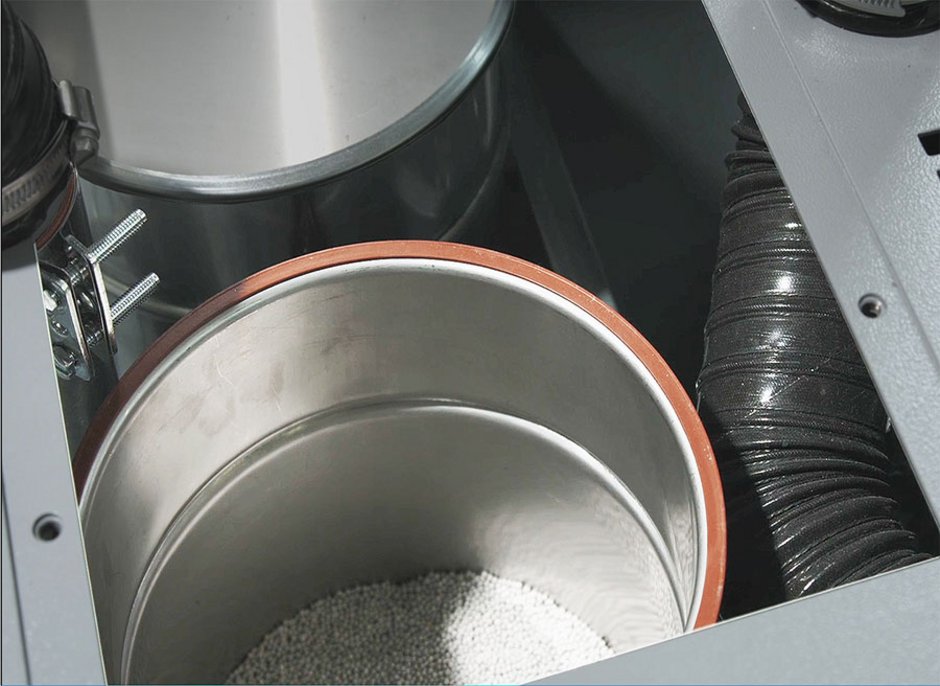
La comparación de los sistemas de secado convencionales con diseños modernos ilustra varios enfoques para ahorrar energía. En particular, un control del flujo de aire, tal vez combinado con una reducción de temperatura, así como el uso de intercambiadores térmicos en aplicaciones de regeneración y alta temperatura son en este contexto equipos adicionales muy valiosos.
El consumo total de energía durante el secado se basa esencialmente en los requisitos de energía de los siguientes elementos consumidores individuales:
- Proceso de calefacción
- Regeneración del desecante
- Motor Soplante
- Enfriamiento del aire de proceso de retorno (optional)
Además, el consumo de energía está influenciado significativamente por parámetros materiales tales como:
- Carga de material y temperaturas establecidas en tolva de secado
- Entrada y contenido nominal de humedad humedad residual
- Rendimiento
- Tipo de materia prima
- Entrada de material y temperaturas establecidas.
Además, los parámetros relevantes para el consumo energético de una línea de secado son:
- Caudal de aire seco
- Tipo de regeneración
- Temperatura del aire de proceso
- Sistema de recuperación de calor, así como la
- Pérdida de calor
El consumo adicional de secadoras que utilizan tecnología convencional puede afectar al consumo de energía en todas las áreas. El motivo es porque los sistemas de secado deben diseñarse de tal manera que incluso en las peores circunstancias posibles, los valores nominales sean alcanzados. Entonces, en el momento en que parámetros como por ejemplo la humedad inicial, la temperatura de entrada o el rendimiento del material “mejoren” , se podría teóricamente reducir el suministro energético.
En sistemas sin control del caudal de aire, se introduce demasiado aire a través de la tolva de secado. Esto tiene un efecto directo sobre el consumo de energía de las tolvas de secado, que por lo tanto requieren más energía de la necesaria para el calentamiento del equipo.
Con un control del caudal de aire en verano – debido a la temperatura más calida de entrada del material – se puede reducir directamente el consumo durante el proceso. Este consumo de energía en verano puede ser reducido hasta en un 25%.
En general, por supuesto, hay otras formas de ahorro de energía. Como por ejemplo por disminuir el rendimiento por cuestiones de producción, o durante los fines de semana al reducir la producción. Gracias a un control del caudal de aire, el flujo de aire se puede reducir hasta aproximadamente un 40%, lo que también reduce notablemente el consumo de energía.
Por lo general, el consumo de energía de los motores soplantes es del 60% de la potencia de conexión. Si el caudal de aire del soplante de proceso se reduce mediante un control de flujo de aire, el consumo de energía del soplante también se reduce. En este contexto, un aspecto importante juega un papel crucial: la resistencia a la presión en las líneas de aire aumenta cuadráticamente con la velocidad del aire. Por el contrario, esto significa que si el caudal de aire se reduce a causa de una menor velocidad del soplante, el consumo de energía también disminuye de forma cuadrática. Al mismo tiempo, todo el sistema de línea de un sistema de secado se verá equilibrado. Las fugas en el sistema de tuberías tienen un menor efecto en el caso de un caudal de aire más bajo, ya que la menor diferencia de presión con el medio ambiente provoca que entre menos aire del exterior al sistema de secado, lo que a su vez reduce el contenido de humedad del tamiz molecular.
Si el equipo funciona únicamente con un método de regeneración simple y sin control del punto de rocío, la regeneración del tamiz molecular se cronometra en tiempos de ciclo fijos. El estado real del tamiz molecular no tiene importancia.
Un proceso de regeneración optimizado, por otra parte, consume sólo la energía necesaria para el ciclo de regeneración real. Además, con un intercambiador térmico en el circuito de calefacción de regeneración puede ahorrar hasta un 25% de energía de calefacción.
Ejemplos de comparación de parámetros seleccionados de una sistema de secado convencional y controlado para cinco materiales
- ABS: 45 kg/h
- ABS: 40 kg/h
- PA 6: 60 kg/h
- PC / Disc: 50 kg/h
- PSU: 25 kg/h
- Potencia de calentamiento requerida en las peores condiciones: 5,55 kW
- Requerimiento de aire calculado: 380 m³
- Secador seleccionado: 400 m³ rendimiento de aire
- Rendimiento de deshumidificación requerido: máx. 1000 g/h
Regulada | Convencionalmente | |
Requerimiento de aire seco | Variable hasta 380 m³ | Variable hasta 380 m³ |
Producción de aire seco | Siempre 400 m³ | En función de la demanda 120 -380 m³ |
Ciclos de regeneración | En función del tiempo cada 3 h | En función de la demanda aprox. cada 4,4 h |
Energía de calefacción | Aprox. 6 kW | En función de la demanda aprox. 2,2 – 6 kW |
Consumo de energía del soplador | Constante 2,2 kW | En función de la demanda aprox. 0,7-2,2 kW |
Temperatura de aire de proceso | En función del caudal | Casi constante |
Regeneración intercambiador térmico | No | Si, hasta un 25% ahorro de energía / ciclo |
Demanda energética para reducción del rendimiento | Constante | Se reduce |
¿Cómo pueden las diferentes combinaciones de equipos lograr el mejor proceso de secado? Puede encontrar más información sobre secado en www.motan.com